RESOURCES
EMC Considerations for Electric Vehicle Charging
The electric vehicle (EV) market has skyrocketed since it emerged in the 2010s. In the last decade, the number of passenger EVs has gone from virtually zero to over 10 million. They've become so popular that charging stations are now getting more commonplace. These can now be found in the parking lot of your local grocery store, parking garages, and provided by the city.
With the increase in the number of charging station installations, the impact of electromagnetic interference (EMI) becomes imperative as it can impact the performance of both the charger and the vehicle.
Exploring EMI in Electric Vehicles Charging Stations
The first charger designs were low-power slow chargers; Level 1 (1.8kW, 120VAC) and Level 2 (3.9~19.2kW, 240VAC. With EVs getting more popular, the limited battery range posed a need for faster charging paving the way for high-power Level 3 DC chargers (24~300kW, 400~900VDC). Now as bigger vehicles such as buses, trucks, forklifts, and delivery vehicles are getting mainstream, wireless induction charging is getting more popular.
The high-power DC chargers employ 3-phase input and high voltage DC output utilizing AC-DC and DC-DC power conversion circuits to deliver more power to the EV. In induction chargers, AC power is induced into an onboard coil by large offboard coils. As power coming into the vehicle is AC, the power conversion (AC-DC and DC-DC) is done onboard the vehicle.
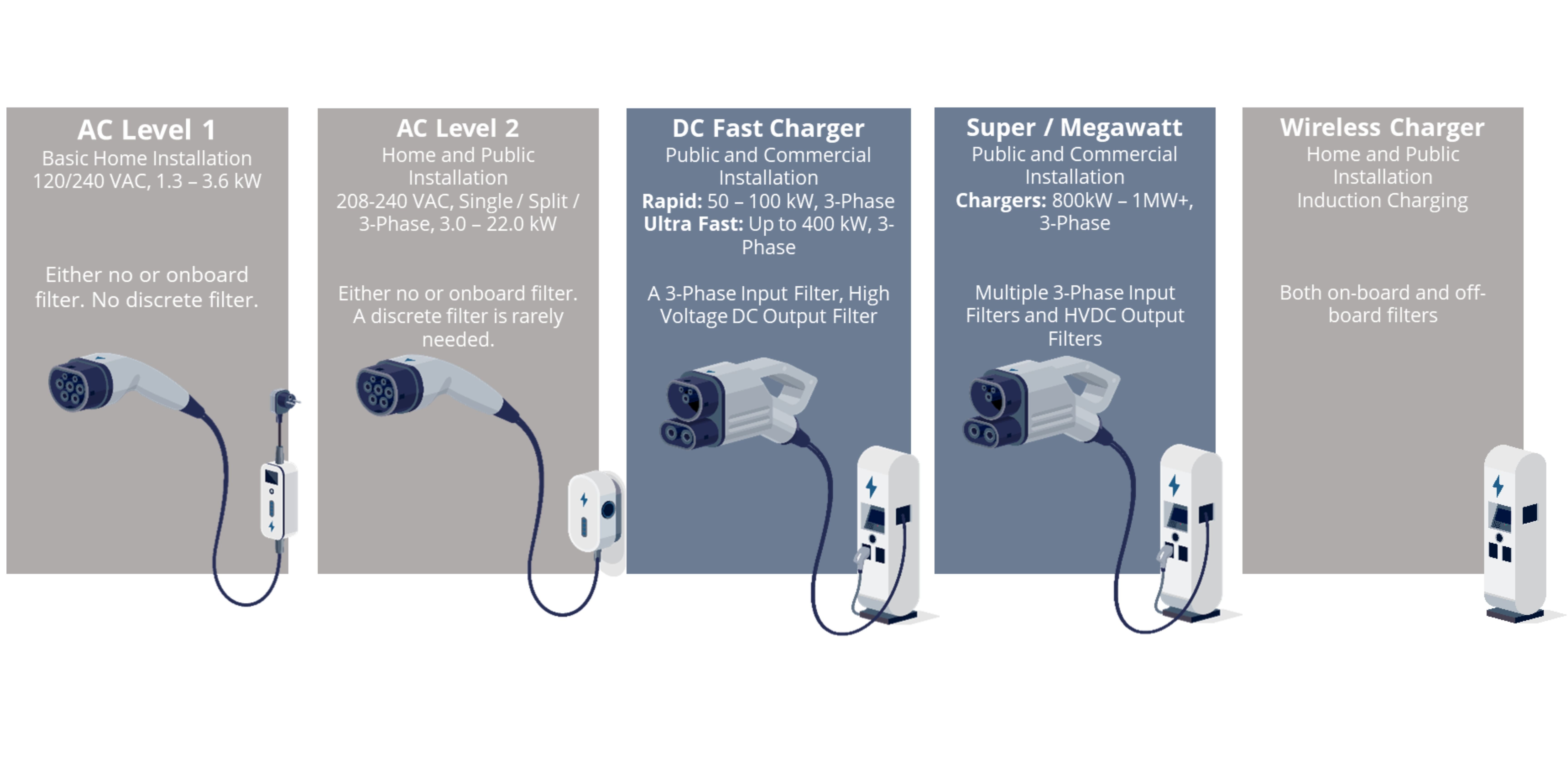
When an EV is plugged in, there’s a communication process before the charger is energized. The charger communicates to the car the maximum power it can deliver, and then the car calls for the power that the station can deliver, and the vehicle can accept. EMI can affect the communication process as well, especially, silicon carbide and gallium nitride devices that generate harmonics in 2.4 and 5 GHz frequency bands.
Why EMC Designs Are Crucial to EV Charging Stations
With many EMI-producing components in highspeed DC fast chargers, EMC becomes an essential design consideration. The high-power electronic circuits produce sensitive signals and rely on their integrity to correctly carry out their intended functions. EMI can corrupt or interrupt the useful signals which can disrupt circuit performance and outputs.
The noise produced can also propagate outside the EV chargers impacting the facilities and equipment in the vicinity. In addition to that, EVs have a large magnetic field generated by the battery, motors, and power circuits. This field can also impact the fast charger and vice versa. In the case of induction charging, the noise is generated by onboard power conversion electronics. This makes interference with other onboard electronics a lot easier, a major challenge for EV design engineers.
EMI-compliant designs need to both prevent EMI from being emitted from a device while protecting it from EMI emitted from other devices. To effectively accomplish this EMI suppressions (common and differential modes) must be included at the input and output of every power conversion stage (AC-DC, DC-DC, etc.). In addition to that, power line EMI filters and shielding create an effective barrier for the EMI to the outside world, both onboard and offboard. EMI filters mitigate conducted emissions over the power lines whereas shielding prevents radiated EMI, making them a useful part of an EMI compliant design.
Designing EMI Compliant EV Charging Stations
EMI compliance for EV (DC fast) charging stations are mandated by a number of regulations and standards developed by various International Standards Organizations, so engineers need to consider EMI compliance from the preliminary design stage of the project. Different countries have their own standards, but many of these have been harmonized. The United States and Canada, for instance, both use class-based systems that cover EV charging in different environments.
Some of the commonly used standards are.:
FCC Part 15 Part B - Class A / Class B: This EMC standard is primarily used in North America. Class A is the least stringent of the two and covers commercial, industrial, and business environments. The strength of the electromagnetic field cannot exceed specified limits at 3 meters from the device. Class B is more stringent which applies to chargers used in residential applications. The conducted emissions limits are tighter and radiated emissions are tested 10 meters away from the device.
- IEC 61851-21-2: Electric vehicle conductive charging system: Electric vehicle requirements for conductive connection to an AC/DC supply. This International Electrotechnical Commission (IEC) standard outlines EMC requirements for offboard electric vehicle charging systems
- IEC 61851-23: Electric vehicle conductive charging system: DC electric vehicle charging station. Communication between EV and DC EV charging station
- CISPR 11/EN 55011: This European standard provides limits and methods of measurements for emissions that apply to industrial, scientific, and medical equipment
- CISPR 22 / EN 55022: This standard provides limits and methods of measurement for emission for Information Technology Equipment.
For DC fast charger to comply with conducted emissions, a 3-phase EMI filter must be put at the power input. As the charger power output increases the noise levels tend to increase making it necessary to use a dual-stage filter design. Similarly, the noise at DC output can exacerbate radiated emissions. In such situations, in addition to system shielding, a high voltage DC-filter must be placed at the fast charger output to reduce radiated emissions. In induction-charged vehicles, the DC filter is placed onboard between the DC-DC converter and the battery charging stage.
EMC solutions can come with a range of trade-offs, which is why it's such an important consideration in the design process. Many filtering solutions take up a lot of space or add undesirable weight. In such cases, a compact, low-weight EMI/EMC filter similar to the ATDI RP695 series (450A - 1600A, 1500VDC, dual-stage) becomes necessary. For special applications requiring unique form factors or insertion loss characteristics, modified standard or custom designs are done to meet space and performance requirements.
EV Charger Safety
DC fast charger output a high voltage DC for fast charging. This adds a safety challenge to the charger design. IEC 61851-1 covers all safety European safety requirements that a charger must meet including the degree of protection, creepage and clearance distances, temperature rise, protection against electric shock, protective circuit integrity, connection protocols, and in-rush current. In the US UL2202 and UL 2251 cover similar safety requirements for EV chargers and connection components (plugs, receptacles, couplers).
In addition to these, the galvanic separation between the input and output sides of charging stations is also a key requirement. Galvanic separation prevents electric conduction between two electric circuits that exchange power and/or signals - in this case, the charging station and the vehicle. Galvanic isolation is a design technique that separates electrical circuits to eliminate stray currents. Signals can pass between galvanically isolated circuits, but stray currents, such as leakage current, differences in ground potential, and/or induced currents, are blocked.
Astrodyne TDI's EMC Solutions
Astrodyne TDI has been designing power and EMI filter solutions for over 60 years. We provide power supplies and filters to a wide range of demanding applications and power needs such as EV charging, alternative energy, medical, industrial equipment, automation, MRI room, and secure facilities. With ISO 9001- and ISO 13485-certified facilities and a team of experienced engineers on hand durability and quality are at the heart of our products, They can help you find the right AC and DC filter solution for EV chargers, or designs a cost-effective custom solution
To learn more about Astrodyne TDI's capabilities or discuss EMC solutions with a pro, reach out to us today!